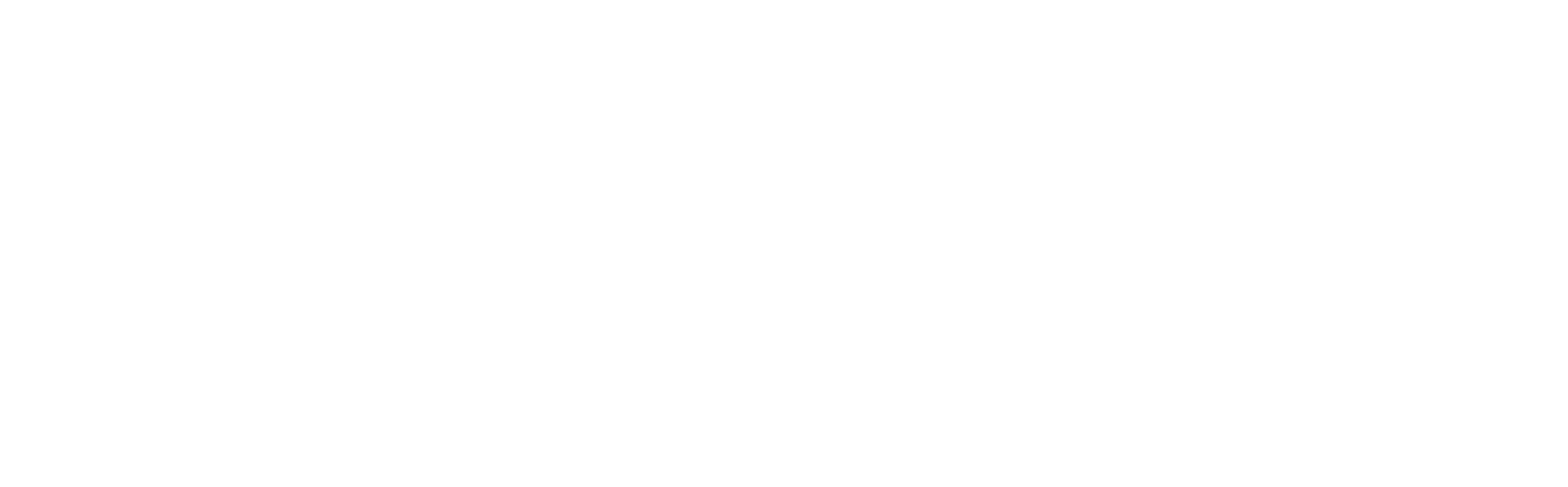
coke drum services
Coke drum services address coker-specific challenges with advanced weld automation
For decades, WSI has provided advanced coke drum services and repair options to address prevalent coke drum failures. Our unique process uses highly engineered weld metal overlay to modify the vessel’s structure, mitigating bulging and cracking of the pressure boundary shell, support skirt-to-shell interface weld area, and lower cone cladding damage. As the industry’s largest provider of structural repairs for coke drums, WSI excels in coke drum maintenance and coker drum repair.
Our process involves installing a highly engineered weld metal overlay on existing vessels and modifying their structure to mitigate bulging and cracking caused by low-cycle fatigue.
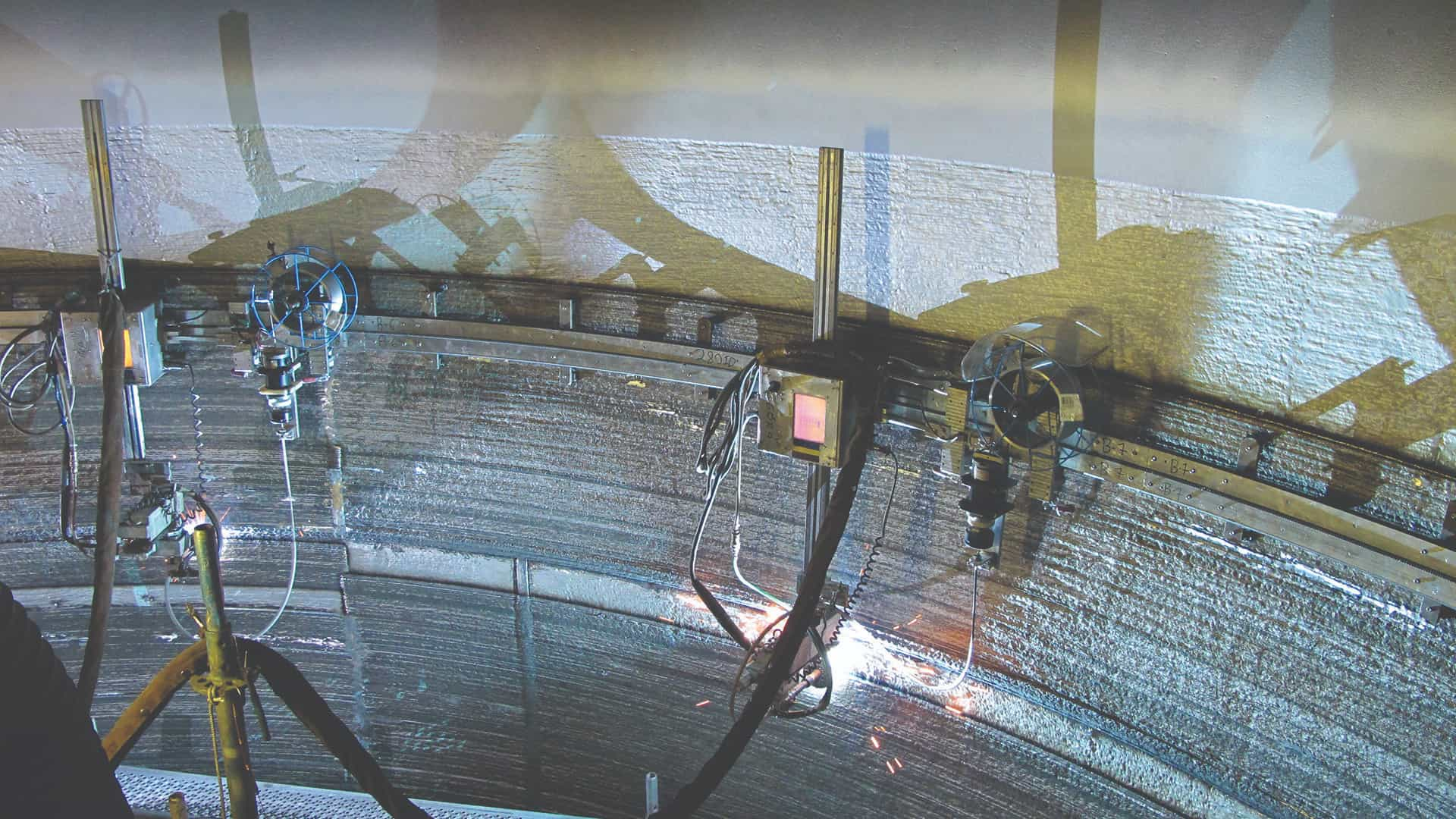
Precision weld automation for optimal coker drum repair
Our tightly controlled welding parameters, managed by closed-loop automated welding systems, employ controlled deposition techniques (temper bead) to eliminate the need for post-weld heat treatment. This approach has been successfully implemented in over 100 coke drums worldwide, ensuring reliable coke drum automated weld overlay repairs.
For support skirt crack repairs, WSI uses proprietary welding processes to replace critical welds and install new skirt sections without post-weld heat treatment. This method has been proven superior, with dozens of successful skirt repairs across the industry.
WSI engineered solutions for coke drum reliability
Delayed coking, which has been in use since the 1950s, subjects components to significant temperature and pressure fluctuations, causing low cycle fatigue failures in coker drums. These drums are costly to replace and are critical assets, making life extension, shortened turnaround cycles, and improved reliability and safety essential.
As the largest provider of structural repairs for coke drums, WSI extends life, shortens turnaround cycles, and enhances the reliability and safety of these critical assets through our automated coker drum weld overlay.
- Bulge repair and structural shell reinforcement
- Lower cone replacement welds utilizing the HotPulse® critical weld process
- Shell and support skirt crack repair
- ID cladding damage and defect repair
With our extensive experience and cutting-edge technology, WSI provides industry-leading coker weld overlay repair and coke drum services, ensuring the highest quality and reliability for your critical assets.
Contact Us
Downloads
Locations
Follow WSI
Related Featured Stories
Delayed Coking Unit (DCU) Process, Thermal Cycling and Bulge Mitigation Techniques
Beginning in the early 1990’s, WSI initiated the first Structural Weld Overlay’s (SWOL) in coke drums. With aid from partners in the industry, SWOL process was developed as an engineered repair method utilizing advanced techniques in laser mapping, fatigue analysis, and field machine welded execution.
Engineered Repair Innovations in Delayed Coke Drums
Overview of Delayed Coking Units, Skirt Design Challenges, and Skirt to Shell Fatigue. By Ian J. Gilpatrick MBA, MSc
WSI’s HP GTAW™ Machine Welding for Coker Cone Modifications
The Faster, Safer and Better Automated Approach for Coke Drum Cone Modifications.
Furnace Tube Welding
Advanced furnace tube welding technology for challenging u-bend welds in heaters and furnaces
Piping Services
Piping services with revolutionary machine orbital welding for planned or emergent outages
Superheater, Reheater, and Economizer Services
Over 30 years of experience in superheater, reheater, and economizer services
Waterwall Services
World’s largest installed base for the mitigation of fireside corrosion