E-Series explosion-proof LED wallpack linear lighting for hazardous-rated environments
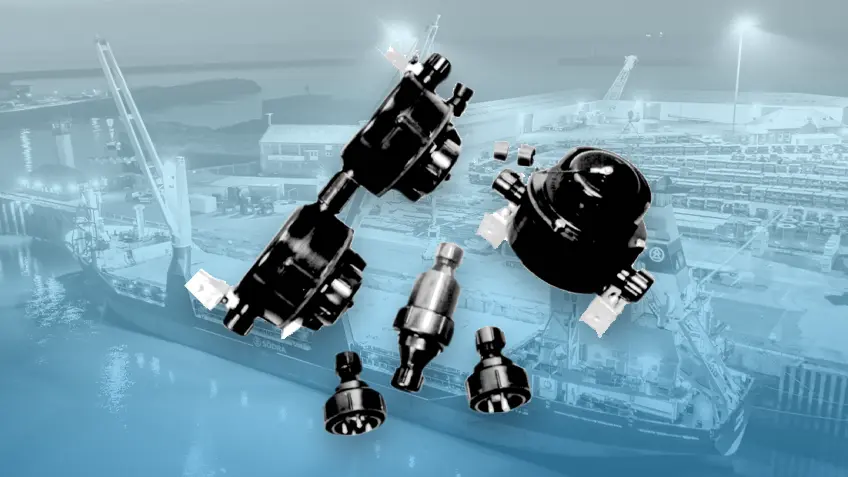
RIG-A-LITE wallpack lighting delivers durable, energy-efficient illumination for industrial and hazardous locations. Designed for wall or flat-surface mounting, these fixtures ensure reliable performance in tough conditions. Features like explosion-proof construction, impact-resistant lenses, and versatile beam angles enhance safety and visibility. Ideal for building perimeters, walkways, and confined spaces, wallpack lighting provides dependable, cost-effective solutions.
E-Series explosion-proof LED wallpack linear lighting for hazardous-rated environments
The posts you requested could not be found. Try changing your module settings or create some new posts.
Ruggedly constructed power distribution centers for industrial and power generation applications
Customized protection and control panels to meet your current and future requirements
RIG-A-LITE clean room lighting provides superior illumination for environments requiring strict contamination control, such as pharmaceuticals, semiconductors, laboratories, and healthcare facilities. Designed to meet the needs of hazardous locations, clean room spaces, and sanitary applications, these lighting fixtures offer watertight integrity, easy installation, and reliable performance. Engineered for demanding settings, including ISO Class 3-9 clean rooms and BSL 3 & 4 laboratories, our clean room lighting ensure safety, durability, and compliance.
The posts you requested could not be found. Try changing your module settings or create some new posts.
Ruggedly constructed power distribution centers for industrial and power generation applications
Customized protection and control panels to meet your current and future requirements
RIG-A-LITE offers NSF-rated lighting specifically engineered to withstand the demanding conditions of food processing environments. Food processing activities can present difficulties for lighting systems because of extreme heat, the presence of grease, oil, and various contaminants, the application of strong cleaning agents, and high-pressure cleaning methods. RIG-A-LITE NSF-rated lighting is built to endure these challenging environments, ensuring long-lasting performance. Our LED technology provides energy-efficient, bright illumination, enhancing visibility and safety in food processing facilities. Backed by a 1- or 5-year warranty, RIG-A-LITE NSF-rated lighting solutions deliver unmatched reliability, even in the harshest conditions.
NSF-certified fluorescent linear lighting with emergency backup for food processing
NSF-certified LED linear lighting for high-pressure cleaning and wet locations
NSF-certified fluorescent linear lighting with watershed design for demanding conditions
NSF-certified LED high-bay area lighting with debris-shedding design for harsh environments
Explosion proof NSF-certified LED high-bay area lighting for harsh and hazardous locations
Explosion proof fluorescent linear lighting for hazardous locations and wet environments
Explosion proof LED linear lighting for hazardous locations, wet environments, and sanitary applications
NSF-certified fluorescent high-bay lighting for harsh wet environments
LED non-metallic enclosed and gasketed linear lighting for demanding applications
Explosion proof NSF-certified high-bay fluorescent lighting for hazardous locations
Explosion proof NSF-certified high-bay LED lighting for hazardous locations
NSF-certified high-bay fluorescent lighting for heavy hose-down environments
NSF-certified LED high-bay lighting designed for heavy-hose-down and wet environments
The posts you requested could not be found. Try changing your module settings or create some new posts.
Ruggedly constructed power distribution centers for industrial and power generation applications
Customized protection and control panels to meet your current and future requirements
RIG-A-LITE’s general-purpose industrial lighting provides superior illumination and maximum durability for non-hazardous applications where ATEX, UL, and ETL certifications are not required. Our LED fixtures are purpose-built to ensure safe, reliable lighting with high efficiency and flexibility. RIG-A-LITE’s expertise in various environments and exceptional technical support guarantee optimal product selection for any setting.
Low-profile energy-efficient LED area lighting for demanding environments
Hi-lumen LED wide-area lighting designed for demanding environments
Compact low-profile LED area lighting for tough industrial conditions
Non-metallic heavy duty LED Lighting for marine locations
Explosion proof clean room LED linear lighting ensures compliance in controlled environments
Clean room LED linear lighting optimized for sanitary applications
E-Series hazardous-rated LED emergency light and exit sign for challenging environments
E-Series modular LED stadium flood light for harsh locations
E-Series LED high-temperature high-bay lighting for harsh locations
NSF-certified fluorescent linear lighting with emergency backup for food processing
NSF-certified LED linear lighting for high-pressure cleaning and wet locations
NSF-certified LED high-bay area lighting with debris-shedding design for harsh environments
Explosion proof NSF-certified LED high-bay area lighting for harsh and hazardous locations
UFO LED high bay light provides energy-efficient illumination for harsh environments
Low-profile LED area lighting designed for marine, wet, and industrial environments
Compact high-bay LED flood lighting for harsh environments
Low-profile LED linear lighting ensures reliable performance in harsh environments
NSF-certified fluorescent high-bay lighting for harsh wet environments
LED non-metallic enclosed and gasketed linear lighting for demanding applications
RIG-A-LITE Products continues to set the standard for exceptional lighting solutions with the release of upgraded lumen packages - providing output and efficiency as high as 25,940 lumens at 194 watts (LHFL/LFL) and 16,420 lumens at 127 watts (LHFLJ/LFLJ).
Ruggedly constructed power distribution centers for industrial and power generation applications
Customized protection and control panels to meet your current and future requirements